ACTUATORS
AMPLIFIERS
NI SbRIO
Hardware
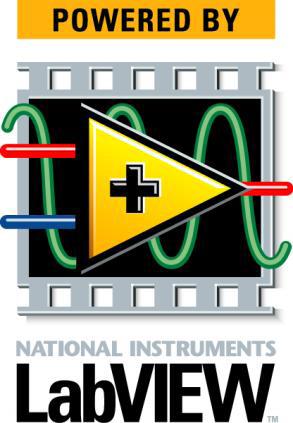
Brushless DC motors were chosen for actuators because they: 1. Have built-in sensors for feedback and precise torque control.
2. Reduce noise and
operate more smoothly than brushed motors.
3. Are representative of the quality standards in aerospace applications.
The motors that were used are rated at 36V with a rotary speed of 10,000 RPM and peak torque of 416.6 oz-inches. Each motor has integrated Hall Effect sensors and a 71:1 reduction planetary gearbox.
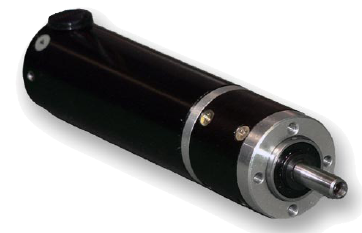
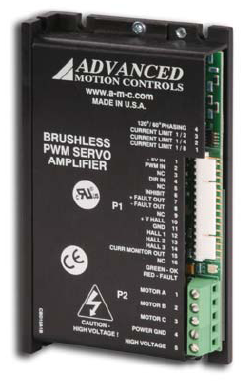
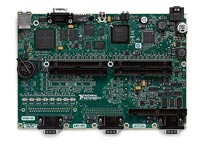
The specifications of the servo amplifiers are governed by the specifications of the brushless DC motors. The motors require 3-phase power with a maximum current load of 4.1 Amps and peak power of 41.88 Watts. The amplifiers take feedback signals from the Hall sensors on the motors and use these signals to provide precise current adjustments for consistent torque. The amplifiers received Pulse Width Modulation and Direction signals from the micro-controller board to determine the speed, torque, at which to drive the motors.
A National Instruments Single-board RIO was used for simplicity of parallel processing and hardware interfacing. When using LabVIEW, the SbRIO allows the programmer drag-and-drop deployment to the microcontroller which greatly expedites compiling and debugging control code. Additionally, the SbRIO has a high speed processor and built-in I/O pins for convenient connection of test wires, ribbons, and connectors. Finally, the board has a built-in Field Programmable Gate Array (FPGA) which allows rapid and efficient management of all I/O ports, PWM generation, and quadrature decoding.